Characterising Powders for Spray Coating Applications 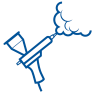
The high performance and low environmental impact of powder coatings make them attractive for a range of applications. Powder coating technology avoids the use of a solvent by fluidising the fine powders used with air, encouraging them to behave in a liquid-like way. While this approach confers environmental advantage, avoiding the volatile organic emissions associated with solvent use, it presents the challenge of ensuring that the powder flows easily and smoothly during application. Demand for thinner films that necessitate the use of ever smaller particles intensifies pressure on powder flowability, as interparticle forces of attraction increase dramatically with decreasing particle size.
Powder coating production involves the melt blending of polymers/resins with a range of additives, followed by extrusion, and grinding of the extrudate to the required particle size. Powders are manufactured and delivered in batches to allow close matching of customer requirements with powder properties, although additives may still be incorporated immediately before application to change specific aspects of the final finish.
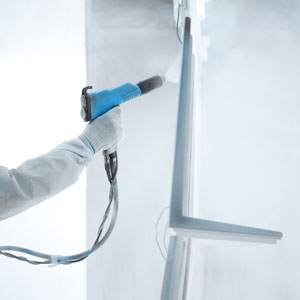
Coatings are applied to a substrate either in a fluidised bed or more commonly using spraying processes. Prior to spraying, powder is fluidised in a hopper to ensure smooth consistent flow to the gun. During spraying the powder becomes charged, encouraging adhesion to an earthed substrate. Any powder that does not adhere is recovered and recycled to significantly improve utilisation and minimise waste. The substrate is cured at high temperature to allow the discrete particles to fuse and form a smooth finished film.
Powder recycling is a critical process where problematic powder flow can be particularly detrimental. Although the particle size properties of a virgin material may be accurately defined, attrition during the spraying process is likely to have an impact on particle size and/or morphology. Mixing the recovered material with virgin material, in varying ratios, means that the process is typically operating with material that has very different properties to the well-defined virgin material. The ratio of virgin to recycled material is therefore one of the variables commonly manipulated to address flow issues.
Take a look at our latest 2023 App Note on Batch Variability in Spray Coating
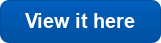
The factors that can influence powder flow properties are:
- Particle size
- Particle shape
- Hardness
- Porosity
- Surface roughness
- Moisture content
- Segregation
- Aeration
Identifying and quantifying which properties correlate with the most efficient performance in a process allows new formulations to be optimised without the significant cost of running samples through the process to assess suitability, making considerable savings in terms of time and raw materials, and minimising wastage due to rejected products.
The study, in the banner below, shows how the FT4 Powder Rheometer®, a comprehensive powder characterisation tool, has identified clear and repeatable differences between the three powder samples in terms of Dynamic and Bulk properties, which correlate well with in-process performance.