Understanding Powder Behaviour in Battery Materials 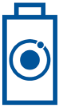
Lithium-ion (Li-ion) batteries are used in a wide range of products that require a rechargeable power source due to the fact that they have high energy density, resistance to self-discharge, and minimal memory effect. This makes them attractive for use in consumer electronics, power tools, automotive and aerospace applications.
Figure 1 shows the typical process steps involved in the production of Li-ion batteries. The various stages within the process are highly dependent on the quality of the slurry produced at the start of the process.
The properties of the slurry will in turn depend on the properties of the powder mixed with the binder and solvents, and how it behaves in the mixing process.
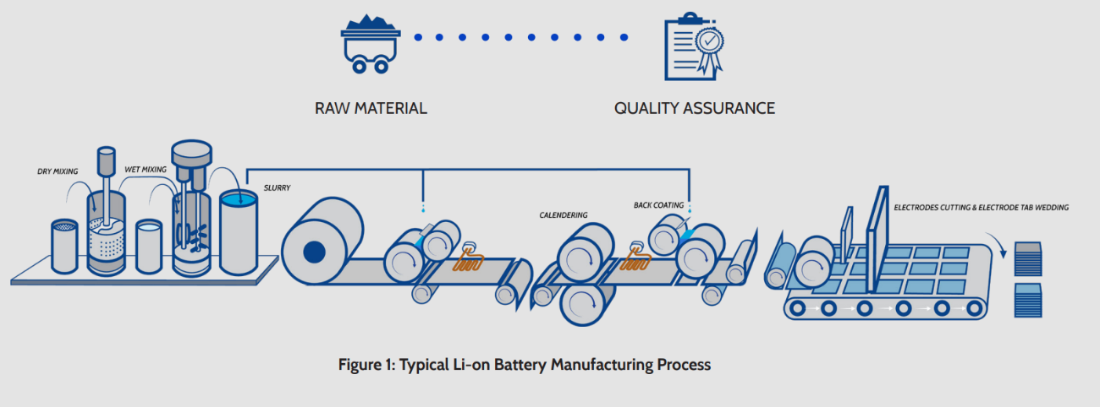
The resulting slurry must meet critical criteria such as fineness of grain (FOG), viscosity and solid content to ensure optimal process performance as well as a high-quality final product. In particular, solid content uniformity influences how efficiently a slurry coats a substrate so the ability of the powder to mix and disperse, without agglomerating, is critical.
Process relevant powder characterisation
The rheological properties of a powder that dictate how well it mixes and disperses to form a slurry, are the same properties that determine flow behaviour and influence factors such as agglomeration. The data in Figure 2 illustrates how properties measured using the FT4 Powder Rheometer® correlate with in-process experience in the manufacture of Li-ion batteries.
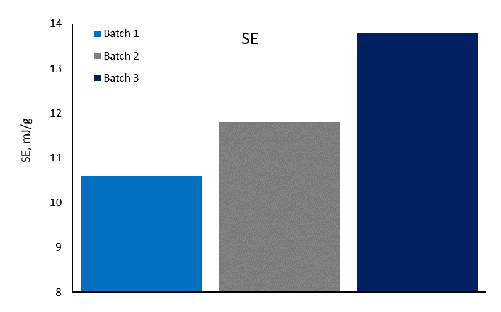
Figure 2 - Specific Energy (SE) for 3 batches of LiFePO4 used in the production of Li-ion batteries
Three batches of LiFePO4 from different suppliers were used to produce anodes. Batch 1 was known to produce a homogeneous slurry whereas Batch 2 and Batch 3 were more inconsistent and also resulted in blockages leading to system downtime and out of specification products.
SE quantifies the degree of mechanical interlocking and friction between particles. The low SE value for Batch 1 suggests that the particles can disperse more freely and are less likely to bind together to form agglomerates.
Permeability describes the ability of a powder to release or retain entrained air. The higher Pressure Drop recorded for Batch 1, indicating lower Permeability, is likely to be a consequence of a more efficiently packed bed. Powders that exhibit a more regular packing structure are typically more free-flowing and consequently able to disperse more freely and uniformly. The lower cohesion strength also reduces the risk of agglomeration.
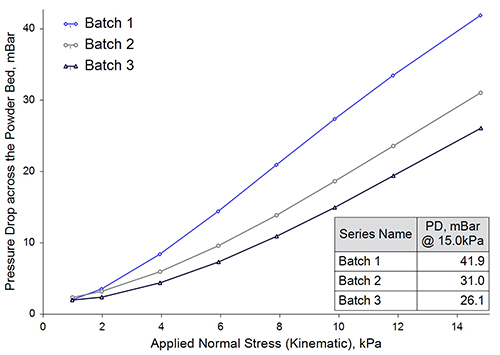
Figure 3 - Permeability (expressed as a Pressure Drop) for 3 batches of LiFePO4 used in the production of Li-ion batteries
The results suggest that less permeable powders, with a low degree mechanical interlocking and friction are conducive to producing a homogeneous slurry for use in manufacturing electrodes for the production of Li-ion batteries. The multivariate approach of the FT4 Powder Rheometer enables these properties to be accurately quantified allowing robust powder specifications to be defined.
View our latest case study on how to improve Battery Performance.
For more information on the range of analytical equipment, offered by Micromeritics, which can improve your lithium-ion battery’s safety, energy & power density, and cycle life, please go to - micromeritics.com/lithium-ion/