The Importance of Powder Flow in Additive Manufacturing 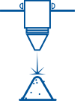
Additive Manufacturing (AM), also known as 3D printing, is a potentially transformative manufacturing technique. This process involves printing intricate, components to a tight specification which demands a high degree of consistency and repeatability in the feedstock. Controlling the performance of the powders is critical for both process efficiency and final product quality. How the powder is spread and distributed, as the layers are formed, are defining aspects of this performance. Variability in feedstock can lead to inconsistent bulk density, non-uniform layering, low tensile strength, poor surface finish and other part defects.
The extent to which AM will shape the industrial landscape depends on the development of high-speed, precision machinery, and on the identification and consistent supply of powders able to meet the exacting demands of these machines. Increasingly the focus is turning to the powders themselves and how they can be optimised in an intelligent and reliable way. Powder characterisation has a vital role to play in supporting this process, and testing techniques that can reliably measure properties that correlate directly with AM performance are essential. Identifying which powder properties lead to uniform, repeatable performance of powder allows new feedstocks to be optimised, without the significant financial and time implications associated with running samples through the process to assess suitability, and helps reduce the occurrence of final products that are out of specification.
Take a look at our latest 2023 App Note on Powder Behaviour in 3D Printing
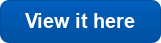
Particle size is often used as a critical quality attribute (CQA), but studies suggest this is not sufficient to fully qualify in-process behaviour, such as powder spreadability. Indeed, it is inadequate to suggest that any parameter from a single test, e.g. Angle of Repose, Hall Flowmeter, Hausner Ratio or Bulk Density measurements, can comprehensively describe how a powder will behave across the range of conditions present in a typical AM process. Furthermore, these traditional techniques are typically too insensitive to accurately identify subtle differences between powders that behave differently in process.
Take a look at our Additive Manufacturing eBook
Download our eBook - Powder Flow Testing for Additive Manufacturing - an engaging, in-depth examination of the role and value of powder testing in AM. The booklet draws together our understanding of the properties that define the performance of powders in AM processes, focusing on the critical issue of powder flow.
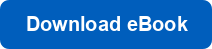
|
The case studies below illustrate the ability of a modern Powder Rheometer to detect minor variations in powders that are directly relevant to powder spreadability and overall performance in AM processes in a way that traditional characterisation methods cannot.
Case Study 1 - Quantifying Batch-to-Batch Variation in Feedstocks
In this first study, the significantly reduced Permeability and increased Specific Energy of one batch of powder demonstrates a clear link to poor spreadability, in particular inconsistent layer uniformity.
The tight tolerances which AM machines operate in mean that differences between batches of feedstocks can lead to significant variability in the properties and quality of the final product. A means of screening each batch before it enters the process can ensure that variation in performance will be avoided.
Three examples of a stainless steel powder from the same supplier demonstrated significantly variable performance in an AM process; Metal Powder A and Metal Powder B both exhibited acceptable behaviour but Metal Powder C regularly caused blockages and poor deposition, resulting in sub-standard final products. All three samples had virtually identical particle size distributions, and demonstrated a similar response in Angle of Repose and Hall Flow tests.
Take a look at our App Note Learning to Predict Print Quality from AM Powder Properties
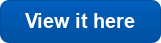
Evaluating the samples with the FT4, however, illustrated several differences between the samples that correlated well with the process performance. During Dynamic testing, the Specific Energy of the samples clearly differentiated Metal Powder C, with the higher value being indicative of increased mechanical interlocking and particle-particle friction. This increased resistance to inter-particular flow is a common cause of blockages and other flow problems in low stress environments.
During Bulk testing, even further differentiation was provided by the Permeability test. Metal Powder C generates a significantly higher Pressure Drop across the powder bed than the other samples, indicating that Metal Powder C is considerably less permeable than Powders A and B. Recent studies have shown that permeability can be critical to the spreading process as it can dictate the formation of air voids within the powder bed.
Case Study 2 - Process-Relevant Differences between Fresh and Used Feedstocks
This second study demonstrates how rheological measurements can be used to identify the optimum blend of Virgin and used material when reusing metal powders to manufacture components.
Powder bed and laser deposition technology both require the use of significant amounts of powder, not all of which becomes part of the finished component. Powder re-use offers the potential to significantly reduce both raw materials costs and overall levels of waste. However, re-use requires careful assessment of the extent to which powders are altered by passing through AM machines, and whether further processing is possible without compromising the quality of the finished component.
A range of different feedstocks containing differing proportions of fresh and used feedstock were evaluated with the FT4’s Dynamic methodology, in an attempt to determine if critical characteristics of the used powder differed from those of the virgin material, and if so, what strategies might be successful in returning the powder to a condition that would enable its re-use.
Comparing the results for the Virgin and Used powders shows that processing has significantly increased the flow energy of the powder. This indicates that the Used powder would not behave the same as the Virgin material and consequently may not perform as well in the process.
Powder exiting an AM machine may contain splatter from the melt pool in the form of larger particles, or may have changed chemically, for example picking up contaminants on the powder surface. Experiments were therefore undertaken to determine whether sieving the Used powder would return it to a state where its flow energy was acceptable. Here sieving improved powder flowability but did not return it to the original flow energy values measured for the Virgin material.
Further experiments were then conducted to see if the Used and Virgin powders could be blended together to form an acceptable feed for subsequent processing. A ratio of 75% Virgin to 25% Used powder produced a flowability most similar to that of the fresh powder, and this blend also exhibited relatively good performance. The 50:50 blend had the highest BFE of all the blended samples, which indicates that flowability does not change linearly with respect to the volume of fresh powder present.
These results highlight the ability of dynamic testing to detect subtle changes in powders that are of direct relevance to their performance in AM machines. As a result, dynamic testing can support successful optimisation and lifecycle management of metal powders for AM, in a way that other powder flow testers cannot.
Please click on the study in the banner below to read more about:
- The effect of additives on the processability of polymer blends used in AM with results highlighting how even small quantities can have a significant effect on the Permeability and Basic Flowability Energy of feedstocks.
- The impact of changing suppliers and/or manufacturing methods of metal AM powders, illustrating how shear properties alone cannot be relied on to identify properties that influence the process.
Copies of the study are available in English, Chinese, German and Japanese, in the 'Featured Downloads' section below.
Further reading: