Analytical Techniques for Successful Cosmetic Compact Manufacture 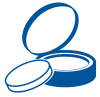
Formulating and manufacturing cosmetic compacts to deliver market-leading performance characteristics requires a high degree of powder processing expertise. The case studies at the bottom of the page consider the measurement of some of the most appropriate properties of both the formulation and the finished product.
Many cosmetics are produced as compacts that, when packaged, are convenient to use and aesthetically pleasing to the consumer. Formulated to give the desired performance in terms of finished effect and ease of application, these discs of compressed powder are typically blends of emollients, preservatives, pigments, fillers and binders. While end-use performance targets tend to be the main drivers in formulation, successful and cost-effective production demands the development of a blend that processes well. Over the long term, the value of a robust manufacturing solution lies in the delivery of consistent product at high throughput and for the least cost.
Compact Manufacture
The first step in manufacturing a cosmetic compact is to blend the dry raw ingredients to acceptable homogeneity and consistency. Adding binder ensures that the powder exiting the blender is cohesive enough to form a stable, uniform compact but remains sufficiently free-flowing to process well in subsequent manufacturing steps. A cone blender, often incorporating a supplementary chopper, is a frequent choice for this application. However, controlling the process to get the ‘stickiness’ of the exiting material just right is not straightforward.
At this preliminary stage it is also important to appreciate that many cosmetic ingredients, such as talc or titanium dioxide for example, are available from multiple suppliers. It is therefore essential to develop specifications that quantify these raw material properties in ways that relate to their performance during manufacture. It is not uncommon for a switch in supplier to result in issues with product quality or production, even though the specification of the new material is ostensibly the same as that of the previous one. Even within suppliers, batch to batch variation can lead to variability. Developing better, more differentiating specifications overcomes these problems.
Filling the compacts is the next stage in the manufacturing process. Here, the aim is to ensure a consistent fill and to avoid segregation or separation of the powder blend. At this point relatively free-flowing materials are advantageous and help to avoid frequent stoppages and incomplete filling. However, if they are insufficiently cohesive, segregation and poor compact strength become more likely, compromising product quality.
The final production step is compression of the powder. Compaction to a stable product of consistent bulk density is essential because the mass of the final product, although the basis for sale, is not directly controlled during manufacture. Compacting a known volume of powder to a consistent bulk density gives a reproducible mass. Properties of the finished compact, such as hardness and strength, are central, directly affecting consumer response, and form the basis of QC testing.
Characterising Cosmetic Powders
Cosmetic ingredients are often specified simply in terms of composition and particle size. These properties are of course important. For example, the particle size of titanium dioxide, which is often used as a pigment or to give opacity, directly influences its optical properties and consequently its performance in the compact. However, the preceding analysis of the steps involved in compact manufacture suggests that other information is necessary to predict in-process performance. The ease with which the raw materials and the blend flow is crucial, as is the formulation’s response to compaction. Defining specifications for these materials in terms of more appropriate powder parameters can therefore pay dividends.
Measuring a powder in motion, using the FT4 Powder Rheometer®, gives a direct indication of flowability, a dynamic material property. With these instruments the axial and rotational forces acting on a blade as it agitates a powder bed are precisely and accurately measured to yield values of flow energy. Well-defined sample preparation techniques, in combination with automated testing methodologies confer a high degree of reproducibility making this analysis sensitive and differentiating. Furthermore, powders can be tested in a compacted, conditioned, aerated, or even fluidised state to fully capture their response to air, a defining characteristic.
Combining dynamic analysis with shear and bulk property measurement builds a valuable toolkit for cosmetic powder characterisation. Shear analysis is a well-established way of quantifying the cohesivity of different materials (the tendency of the particles to stick to each other) and is especially relevant for more cohesive materials. Bulk properties on the other hand, such as permeability, compressibility and bulk density, help to rationalise observed behaviour and provide basic information for process design.
The FT4 incorporates bulk, shear and dynamic testing methodologies, and for cosmetic applications combines them with hardness and pay-off test protocols. Hardness testing across the surface of the compact is a common way of testing the uniformity and success of the filling and compaction process and the integrity of the final product. Pay-off is also a routine test, involving wiping an applicator across the surface of a compact and measuring the amount of powder removed. Traditionally this test is completed by a QA technician and therefore is subject to inter-operator variability. Automation of applied force and shear rate, coupled with more precise mass measurement, gives much more reliable data.
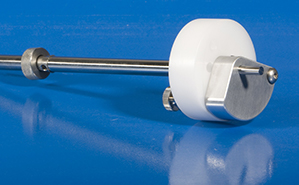
FT4 Powder Rheometer - Hardness Tester
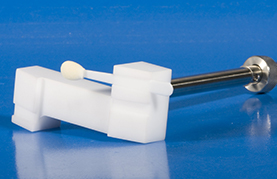
FT4 Powder Rheometer - Payoff Tester
See the Application Note in Featured Downloads (below) to read more about:
- Case study 1 - Controlling the blending process
- Case study 2 - Final compact strength and stability